The most common brazing processes include torch, induction, furnace and resistance brazing. Of these methods, resistance brazing is the least common heating method. Why? Compared to the others, it is a fast and relatively inexpensive process, but limitations in assembly geometry have restricted its practicality. However, today’s technology has expanded resistance-brazing applications to more complex assembly styles.
The Process
Resistance brazing is very similar to spot welding. Both processes heat the base materials by sending direct current through the joint interface. While welding melts the base materials together, resistance brazing only melts the brazing filler metal.
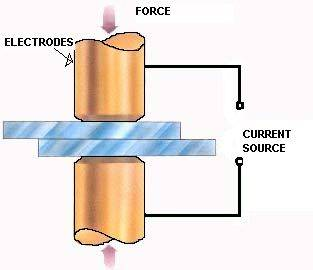
Resistance brazing assembly
Spot welding electrodes meet at a point, but in brazing, there is a benefit to larger surface area contact, so electrodes tend to be flat. You may use high-resistance or high-conductivity electrodes, depending on your base metals. If the base materials are highly conductive, heating may be more efficient with high-resistance electrodes.
The resistance-brazing process involves sending a direct current through the electrodes and the base materials. Resistance to this current by the electrodes, the base materials and their interface causes the base materials to heat to a temperature higher than the brazing alloy’s liquidus. Once this is accomplished, a bond forms.
To Flux or Not to Flux
Manufacturers typically use flux with resistance brazing performed in an open-air environment. Since the process occurs very quickly, minimal flux is required. In some cases, you can braze assemblies without any flux. As it can act as an electrical insulator, avoid flux use if possible.
Common Applications
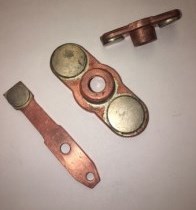
A common application for resistance brazing is the contact industry. Electrical contacts have the perfect geometry for resistance brazing: they are flat. Compositions range from AgCdO to AuAgPt, with the contacts typically bonded to a pure copper lever. Some electrical contacts are silver- or copper-backed to increase wettability in the brazing process.
Contact alloy combinations must have superior electrical properties. Popular brazing alloys in this industry are Lucas-Milhaupt Sil-FOS® 15, SILVALOY® 560 and EASY-FLO®. These alloys have very low melting temperatures, easing the brazing process. You can use the Sil-FOS alloy without flux, depending on the surface characteristics of your contact.
Industry Trends
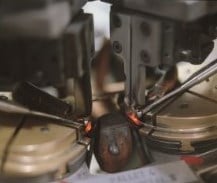
Resistance-brazing technology has expanded over the years - beyond simple flat surface applications to more complex assembly styles. Manufacturers today design electrodes with contours that match the parts being brazed. Product examples include solenoid valves, eyeglass frames and electromechanical assemblies.
Resistance brazing is ideal for a repeatable process and quick cycle time with low thermal distortion. Since the heat is very localized, mechanical properties can be preserved in heat treatable assemblies. Further, there is no need to design an external fixture; the pressure between the two electrodes is usually adequate to hold the assembly.
CONCLUSION:
Limitations in assembly geometry have historically restricted the use of resistance brazing to flat surfaces. Today’s technology has expanded its application to more complex assembly styles.
For further information on resistance brazing, please contact the Lucas-Milhaupt Technical Services Department. Our experts can provide recommendations on the proper brazing processes and braze alloys for your application.
Questions? We are pleased to provide expert information for Global Brazing Solutions® through our blogs and instructional videos. Feel free to share this posting with associates, and save our blog site to your Favorites.
Contact us for further assistance. For detailed questions, call the Lucas-Milhaupt Technical Services Department at 800.558.3856.
Disclaimer: Lucas-Milhaupt, Inc. believes the information contained herein to be reliable. However, Lucas-Milhaupt gives the technical information without charge, and the user shall use such information at its own discretion and risk.